Tri-Layer
The battery separator film is the most important element in a lithium-ion battery.
For public safety, BenQ has both independent and impartial independent verification capability in R&D, production, quality control, and verification of battery isolation films. BenQ is also working with customers and validators from all over the world to achieve the best battery separator film for electric passenger vehicles, large electric vehicles/boats, electric buses, energy storage, and electric tools with the most stringent and continuous validation testing bringing together battery separator products, and customizing battery requirements.
As the only battery separator manufacturer in Taiwan with both technology and medical manufacturing backgrounds, we are committed to the safety of all end-consumers from the perspective of a leader in materials science, working together with industry, government, academia, and research to refine our R&D technology and keep pace with the times, produced and supplied booth in China and Taiwan with fast and best services for all customer.
As the only battery separator manufacturer in Taiwan with both technology and medical manufacturing backgrounds, we are committed to the safety of all end-consumers from the perspective of a leader in materials science, working together with industry, government, academia, and research to refine our R&D technology and keep pace with the times, produced and supplied booth in China and Taiwan with fast and best services for all customer.
Product Categories
Features
Features
Sturcture:BenQ Materials' battery separator manufacturing base covers six core technologies including "roll-to-roll", "polymer structure", "extrusion" and "coating". Each loop construction method affects the battery separator to show the advantages of "high power", "low impedance" and "fast charge and discharge" in lithium-ion batteries, so as to meet the high-efficiency requirements of vehicle use, energy storage and energy storage.
Among them, the "roll-to-roll" precision control ability improves the uniformity of the pores of the separator; the blown film co-extrusion process increases the bonding force between the PP/PE/PP layers and improves the cycle life of the battery cell
The unique pore structure makes the pore size evenly distributed in the battery separator, so that the charge and discharge current is evenly distributed; the product has a low tortuosity, so that the battery separator has low internal resistance characteristics, so that the battery separator using BenQ material has good rate performance, up to Fast charge and discharge performance. The unique "coating" technology can provide the best cost and product efficiency performance in response to customized needs.
BenQ material battery separator has a 135 degree low temperature thermal disconnection (thermal closed cell performance) and a foreign body short-circuit prevention mechanism, which has better safety than competing PE films on the market.
Feature:
- Low film impedance
- High power DCIR
- High safety:
-High strength and crystallinity PP materials
-Thermal shutdown mechanism at low temperature
-Forced internal short circuit inhibition - Long life cycle: Inhibition of structural delamination
-
▲ PP/PE/PP three-layer structure
-
▲ Single layer polypropylene PP structure diagram
-
▲ CCS coating layer top view
Certification
The process is 100% free of metal contamination, a two-pronged approachIn addition to the efficiency of the production, the safety of the battery separator is also given the highest priority by the team.
Full-line, clean room production reduces the impact of dust during manufacturing, while the introduction of AOI high-precision, optical in-line automatic inspection equipment ensures that products can be safely used in batteries without risk of failure or explosion.
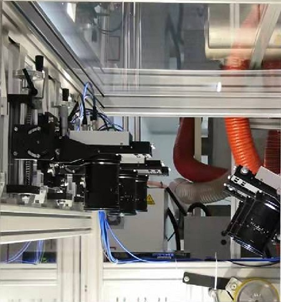
Independent Verification of Quality Control Mechanisms, Stringent Requirements
In contrast to the common one-stop product to quality control, BenQ’s battery separator film quality control is independent and not affected by other units. We strictly abide by customer requirements and ISO, IQC, IPQC, FQC, OQC, and IATF 16949 certifications to ensure that our products are in the best condition to provide customers with peace of mind in the battery and cell manufacturing process.
Specialist Pooling and R&D Focus
The team has invited polymer professionals and experienced specialists from domestic and foreign battery cell factories to continuously adjust the power of battery separators with high porosity and low air permeability to ensure the best low impedance state to refine the power efficiency of battery separators in batteries.
Industry-Academic Cooperation and Technological Advancement
The technology of electric vehicles and energy storage products is improving day by day. BenQ has been working with Taiwan’s Industrial Technology Research Institute (ITRI) and academia to develop and manufacture the best battery separator film products, from the product itself to the optimization of intelligent manufacturing and an MES manufacturing execution system, and has established a leading position as Taiwan’s largest battery separator film manufacturer, providing domestic and foreign battery cell manufacturers with peace of mind and solid support.
Application
The demand for electric energy storage is increasing day by day. In addition to the existing dry process products of BenQ Materials' battery separators, which can be supplied to electric vehicles and electric boats, they will also introduce a wet process layout in the future.Specifications
Mode | D3253 | D3202 | D3182 | D3163 | D3162 | D3161 |
Thickness(μm) | 25 | 20 | 18 | 16 | 16 | 16 |
Gurley(sec.) | 380 | 210 | 200 | 310 | 170 | 140 |
Porosity(%) | 44 | 48 | 50 | 42 | 49 | 55 |
Related Products